LMS Milk Tank - 2
LMS Milk Tank - 2
At last i have ressumed working on the tank wagon following the workshop rebuild.
I think posting photos of a project is a good idea and will try to do that here.
Mean time photos will appear on Flickr
http://www.flickr.com/photos/38139616@N ... 949872919/" onclick="window.open(this.href);return false;
Keith
I think posting photos of a project is a good idea and will try to do that here.
Mean time photos will appear on Flickr
http://www.flickr.com/photos/38139616@N ... 949872919/" onclick="window.open(this.href);return false;
Keith
Re: LMS Milk Tank - 2
Work on the milk tank chassis recommences.


Re: LMS Milk Tank - 2
Leaf springs are progressing well. So well i forgot to take some pictures ! Still I'll grab them tomorrow.
Here are the buckles in various stages of forming.
In the background is the form tool for ensuring they are the right size box.
The vice is set up for drilling the rivet holes. Saves marking out 12 holes.
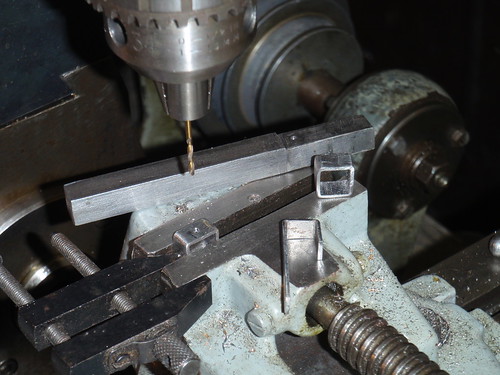
Here are the buckles in various stages of forming.
In the background is the form tool for ensuring they are the right size box.
The vice is set up for drilling the rivet holes. Saves marking out 12 holes.
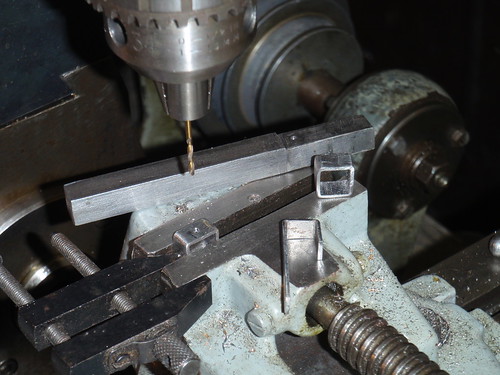
Last edited by Keith1500 on Tue Oct 05, 2010 9:52 pm, edited 1 time in total.
Re: LMS Milk Tank - 2
The sole bar part of the wagon being assembled ready for painting

just learnt this method presents a few difficulties.
1) with the axle guards in place it is very difficult to reach one or two rivets.
2) The head stocks must be attached last. That is to say its best to rivet the sole bar to the frame and do the bracket that attaches the diagonal to the sole, the one that sits just behind the buffer stock. Otherwise once th ehead stock is place the inner most rivets are out of reach !
See Paul's photo of his frame building for the best method. Any comments Paul/Richard?

just learnt this method presents a few difficulties.
1) with the axle guards in place it is very difficult to reach one or two rivets.
2) The head stocks must be attached last. That is to say its best to rivet the sole bar to the frame and do the bracket that attaches the diagonal to the sole, the one that sits just behind the buffer stock. Otherwise once th ehead stock is place the inner most rivets are out of reach !
See Paul's photo of his frame building for the best method. Any comments Paul/Richard?
Last edited by Keith1500 on Sun Oct 10, 2010 2:53 pm, edited 1 time in total.
Re: LMS Milk Tank - 2
Progress being made with the leaf springs.

Tip provided to me by Alan was to be careful when spraying springs. Too much paint could bind them together making them next to useless. I choose to use Humbrol spray and check them for flexing afterwards.

Tip provided to me by Alan was to be careful when spraying springs. Too much paint could bind them together making them next to useless. I choose to use Humbrol spray and check them for flexing afterwards.
Re: LMS Milk Tank - 2
Progess with building the chassis is now focused on fitting the buffers.

If I understood things correctly, taking dimensions from the drawing the 103mm from the face of the buffer to the back of the buffer spring knee should give the correct length buffer (uncompressed).

The mock-up with another wagon show the distance to be good.

If I understood things correctly, taking dimensions from the drawing the 103mm from the face of the buffer to the back of the buffer spring knee should give the correct length buffer (uncompressed).

The mock-up with another wagon show the distance to be good.
Re: LMS Milk Tank - 2
Cross drilling
Certainly got me cross !
My one fear - crossing drilling a small component for a split pin. Whats the secret? Just struggled cross drilling one of the draw hooks and the other one well it broke the drill bit. Broken drill bits are replaceable but the componen with the remains of a drill is the pain.
is the quality of the drills or should i build a spark eroder ?
Keith
Certainly got me cross !
My one fear - crossing drilling a small component for a split pin. Whats the secret? Just struggled cross drilling one of the draw hooks and the other one well it broke the drill bit. Broken drill bits are replaceable but the componen with the remains of a drill is the pain.
is the quality of the drills or should i build a spark eroder ?
Keith
Re: LMS Milk Tank - 2
Keith,
Perhaps you should describe your method for cross drilling then some one might be able to tell you where you are going wrong.
Eddie
Perhaps you should describe your method for cross drilling then some one might be able to tell you where you are going wrong.
Eddie
Re: LMS Milk Tank - 2
In the case of the draw hooks; I faced off a short piece of square mild steel stock and drilled and tapped it 2BA so the hole is nicely down the middle. Then placed it in a vice on the Centec mill and drilled a 0.8mm hole right through the diameter of the 2BA hole.
Then put a 0.8mm pin through the hole, screw in the draw hook till it touches, remove the pin, rotate the draw hook two turns to the nearest up-right position and we are ready for cross drilling.
The 0.8mm drill seems to start off ok but then feels like its lost its edge. I have tried reshapening but this is hit and miss with a diamond lap at that size. If i persist then the drill breaks.
what do you think?
Then put a 0.8mm pin through the hole, screw in the draw hook till it touches, remove the pin, rotate the draw hook two turns to the nearest up-right position and we are ready for cross drilling.
The 0.8mm drill seems to start off ok but then feels like its lost its edge. I have tried reshapening but this is hit and miss with a diamond lap at that size. If i persist then the drill breaks.
what do you think?
Re: LMS Milk Tank - 2
Wheel Sets

I have machined the axles except for the tapper in to the middle. I'll do this later prior to fitting the wheels.
Also made a start on the wheels by taking a faint skim across the rear boss and then removing 100 thou off the rim. The boss has been drilled out 7.5mm and bored out to suit the axle stubbs.
Question:

End float should the end float on a wheel set be controlled by the boss of the wheel against the axle box or is it the axle withhin the axle box bottoming out on the brearing hole.
If the first option then thats a lot of end float, which is what i have on my Glouster wagon, but runns well and is fine. Is this the norm?

I have machined the axles except for the tapper in to the middle. I'll do this later prior to fitting the wheels.
Also made a start on the wheels by taking a faint skim across the rear boss and then removing 100 thou off the rim. The boss has been drilled out 7.5mm and bored out to suit the axle stubbs.
Question:

End float should the end float on a wheel set be controlled by the boss of the wheel against the axle box or is it the axle withhin the axle box bottoming out on the brearing hole.
If the first option then thats a lot of end float, which is what i have on my Glouster wagon, but runns well and is fine. Is this the norm?
-
- Fat Controller
- Posts: 164
- Joined: Mon Feb 27, 2006 12:38 am
Re: LMS Milk Tank - 2
Hi Keith,
When drilling the drawhooks (which are stainless), you NEED a sharp drill. If it blunts it will rub and work harden the steel which will then be virtually impossible to drill again. As soon as it stops cutting freely, resharpen. A bit of RTD helps. I find the swarf comes off in fairly long curls up the drill flutes and can easily break in the flute and jam, especially if using a drill guide, so clear the swarf regularly, but make sure that when the drill goes back in that it cuts straight away, no rubbing. That might help you drill the hole.
The other problem is breaking through, and I've found that if there is slack between the drill spindle and handle, that as the drill breaks through, it will srew itself through the last bit of material and snap off because the slack in the machine prevents you, or me, from holding the drill back and causing it to cut the full diameter properly. The solution is to remove the slack which could be expensive, though if there is a spindle lock on the drill, you could try putting a bit of load on it, it may help.
I usually machine my wheels and axleboxes so that the back of the axlebox controls the sideplay, don't know what's gone wrong here, have I machined the wheel blanks too thin?. The hole for the axle is meant to be slightly over deep, and can be used as a bit of a reservoir for the first filling of oil. Thin washers can certainly be used to control the sideplay, keep it to a minimum without introducing any tightness on the outer axles, plenty of sideplay on the centre one.
Good work.
Dave.
When drilling the drawhooks (which are stainless), you NEED a sharp drill. If it blunts it will rub and work harden the steel which will then be virtually impossible to drill again. As soon as it stops cutting freely, resharpen. A bit of RTD helps. I find the swarf comes off in fairly long curls up the drill flutes and can easily break in the flute and jam, especially if using a drill guide, so clear the swarf regularly, but make sure that when the drill goes back in that it cuts straight away, no rubbing. That might help you drill the hole.
The other problem is breaking through, and I've found that if there is slack between the drill spindle and handle, that as the drill breaks through, it will srew itself through the last bit of material and snap off because the slack in the machine prevents you, or me, from holding the drill back and causing it to cut the full diameter properly. The solution is to remove the slack which could be expensive, though if there is a spindle lock on the drill, you could try putting a bit of load on it, it may help.
I usually machine my wheels and axleboxes so that the back of the axlebox controls the sideplay, don't know what's gone wrong here, have I machined the wheel blanks too thin?. The hole for the axle is meant to be slightly over deep, and can be used as a bit of a reservoir for the first filling of oil. Thin washers can certainly be used to control the sideplay, keep it to a minimum without introducing any tightness on the outer axles, plenty of sideplay on the centre one.
Good work.
Dave.
Re: LMS Milk Tank - 2
Keith,
If you are wanting to do difficult operations then drilling small holes in stainless steel hits the centre spot.
Dave is right in what he says - sharp drill, regular cutting clearance, plenty of fluid to cool and lubricate, white water does fine for me. Experiment with the drill speed, I would run slower with stainless than for MS. Take some comfort from my father's wise words. "When I have to drill a hole of 1/16th or less I expect to get one hole per drill - any more is a bonus" But then the firm was paying for his and the tool room sharpened them!! Your method is OK except you say nothing about locking the work piece in the jig. Any movement could break the drill. Personally I would want to do the cross drilling before the screw thread is cut because treads are not that tight fitting so the drill has two awkward break throughs to do, but I suspect you don't have the choice with your draw hooks.
On side float, my experience with locomotives and carriages is that there was no intentional float in outside axleboxes, the brass sat between two thrust faces, and any side float, in say the middle axle of a tender was generated by widening the distance between the front and back of the horn flanges. Wagons might be different, but I would have to defer to Dave on that one.
Eddie
If you are wanting to do difficult operations then drilling small holes in stainless steel hits the centre spot.
Dave is right in what he says - sharp drill, regular cutting clearance, plenty of fluid to cool and lubricate, white water does fine for me. Experiment with the drill speed, I would run slower with stainless than for MS. Take some comfort from my father's wise words. "When I have to drill a hole of 1/16th or less I expect to get one hole per drill - any more is a bonus" But then the firm was paying for his and the tool room sharpened them!! Your method is OK except you say nothing about locking the work piece in the jig. Any movement could break the drill. Personally I would want to do the cross drilling before the screw thread is cut because treads are not that tight fitting so the drill has two awkward break throughs to do, but I suspect you don't have the choice with your draw hooks.
On side float, my experience with locomotives and carriages is that there was no intentional float in outside axleboxes, the brass sat between two thrust faces, and any side float, in say the middle axle of a tender was generated by widening the distance between the front and back of the horn flanges. Wagons might be different, but I would have to defer to Dave on that one.
Eddie
-
- Fat Controller
- Posts: 164
- Joined: Mon Feb 27, 2006 12:38 am
Re: LMS Milk Tank - 2
Eddy wrote,
"On side float, my experience with locomotives and carriages is that there was no intentional float in outside axleboxes, the brass sat between two thrust faces, and any side float, in say the middle axle of a tender was generated by widening the distance between the front and back of the horn flanges. Wagons might be different."
You're right Eddy, and wagons were just the same, but on our models we can't do that because we use plain journals, so have to go for the simpler cheat.
Dave.
"On side float, my experience with locomotives and carriages is that there was no intentional float in outside axleboxes, the brass sat between two thrust faces, and any side float, in say the middle axle of a tender was generated by widening the distance between the front and back of the horn flanges. Wagons might be different."
You're right Eddy, and wagons were just the same, but on our models we can't do that because we use plain journals, so have to go for the simpler cheat.
Dave.
Re: LMS Milk Tank - 2
Thanks Dave for your tips on drilling small holes with a sharp drill etc. I think thats where its gone wrong. I let the drill rub and blunten. And Eddie for the concept of using a slow speed perhaps and plenty of lub.
I'd love to get my hands on one of those drill sharpeners that Dereck Brown designed specifically for sharpening small drills on a diamond lap.
Question: when do you sharpen a drill
Answer: after you have used it ! - so one of the C&DMEC chaps once told me .
I'd love to get my hands on one of those drill sharpeners that Dereck Brown designed specifically for sharpening small drills on a diamond lap.
Question: when do you sharpen a drill
Answer: after you have used it ! - so one of the C&DMEC chaps once told me .
Re: LMS Milk Tank - 2
I forgotten what a pleasure it is to machine wheel profiles.

I did these on a mandrel where as my loco wheels i did between centres (once mounted on the axles). This certainly makes turning a lot easier. I have left 10thou on the flanges so these can trued and adjusted once on the axles.

The wheel set components. If you look carefully you will notice one wheel has a larger hole than the other. The corresponding axle side has a 'cock-up collar' silver soldered on it. I should have read Richards words about setting up in the lathe to the front profile, incase the front and back profiles didnt line up too well, which is what happen here.

I did these on a mandrel where as my loco wheels i did between centres (once mounted on the axles). This certainly makes turning a lot easier. I have left 10thou on the flanges so these can trued and adjusted once on the axles.

The wheel set components. If you look carefully you will notice one wheel has a larger hole than the other. The corresponding axle side has a 'cock-up collar' silver soldered on it. I should have read Richards words about setting up in the lathe to the front profile, incase the front and back profiles didnt line up too well, which is what happen here.
Re: LMS Milk Tank - 2
Holes in the Wheels
Question:
A pair on wheels mounted on the axle - Would the holes in the wheels be in line with each other or just ramdon - ie as pressed on but not in line.
Question:
A pair on wheels mounted on the axle - Would the holes in the wheels be in line with each other or just ramdon - ie as pressed on but not in line.
-
- Fat Controller
- Posts: 164
- Joined: Mon Feb 27, 2006 12:38 am
Re: LMS Milk Tank - 2
A pair on wheels mounted on the axle - Would the holes in the wheels be in line with each other or just ramdon - ie as pressed on but not in line.
Don't know with carriage wheels, but Paul Hutfield has looked at lots of photos of wagons with 3 hole disc wheels and concludes that they were in line. But why. Paul reckons it would be easier to lift a wheelset if the holes were in line, but I wonder if it was just the result of the way they were assembled. Wheels were usually pressed on with axle horizontal, and I imagine that the wheels would be lifted to the press using a hook through a hole in the wheel, this would mean that they would all be put in place with one hole to the top, ie in line.
Just checked my photos of the milk tanker at Butterley, they are in line.
Dave.
Don't know with carriage wheels, but Paul Hutfield has looked at lots of photos of wagons with 3 hole disc wheels and concludes that they were in line. But why. Paul reckons it would be easier to lift a wheelset if the holes were in line, but I wonder if it was just the result of the way they were assembled. Wheels were usually pressed on with axle horizontal, and I imagine that the wheels would be lifted to the press using a hook through a hole in the wheel, this would mean that they would all be put in place with one hole to the top, ie in line.
Just checked my photos of the milk tanker at Butterley, they are in line.
Dave.
-
- Fat Controller
- Posts: 178
- Joined: Mon Feb 23, 2009 6:14 pm
Re: LMS Milk Tank - 2
I wondered if it was to detect wheels slipping on axles. If the holes don't like up, one wheel must be rotating free on an axle - or is that even a likely occurrence? The wheel hubs had a driving peg hole, but I assume they weren't turned as a set on a wheel lathe?
Re: LMS Milk Tank - 2
Wheels slipping: I wouldn’t have thought so, not on rolling stock?. it takes a fair few tons of force to push a wheel on to the axle so i wouldn't have thought it could rotate.
Well, looks like I am the one with the wheels which don’t have holes that align !
I quite enjoyed putting together the suspension system yesterday. Those little rubber shock absorbers and the turned caps fitted beautifully and look real good on the J hanger. When fitting the split pins I squeezed up the heads a little to make the head less prominent. nice that the kit included the pins, washers and split pins. Now I have the wheels on I am quite amazed how sensitive the whole suspension system is. work really well. (Compliments to Dave Nobel kit building abilities).
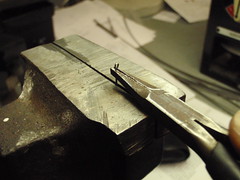
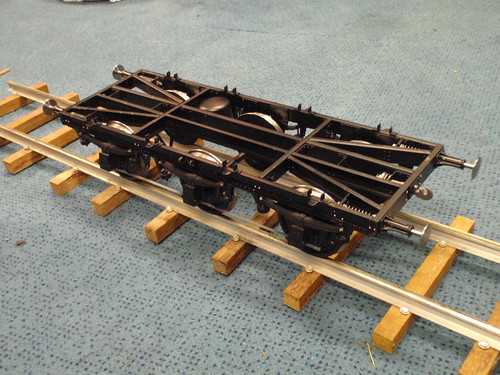
Just working on the axles guard ties.
Well, looks like I am the one with the wheels which don’t have holes that align !
I quite enjoyed putting together the suspension system yesterday. Those little rubber shock absorbers and the turned caps fitted beautifully and look real good on the J hanger. When fitting the split pins I squeezed up the heads a little to make the head less prominent. nice that the kit included the pins, washers and split pins. Now I have the wheels on I am quite amazed how sensitive the whole suspension system is. work really well. (Compliments to Dave Nobel kit building abilities).

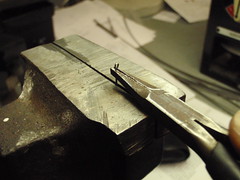
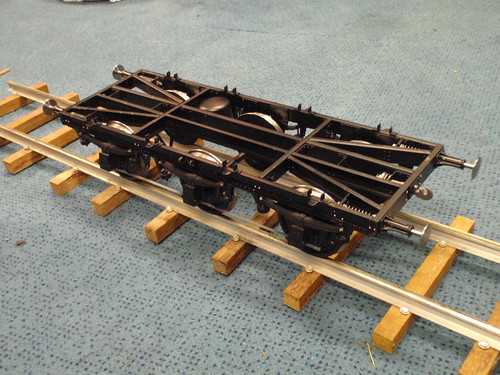
Just working on the axles guard ties.
-
- Fat Controller
- Posts: 178
- Joined: Mon Feb 23, 2009 6:14 pm
Re: LMS Milk Tank - 2
Grand job, and nicely painted by the looks of things, which makes me wonder how you'll attach the splash plates without removing some paint somehow?
I found I needed to extend the brake truss adjustment bars by about a quarter of an inch I think it was to get it to hook up, I'd be interested to see what you find on this. The prototype had a row of three holes in it (or at least the one at the NRM has).
I found I needed to extend the brake truss adjustment bars by about a quarter of an inch I think it was to get it to hook up, I'd be interested to see what you find on this. The prototype had a row of three holes in it (or at least the one at the NRM has).